Occupational Health and Safety
Positioning health and safety as one of the most important priorities in our business activities, we are working to ensure the health and safety of all our employees. To improve health and safety standards, we ensure strict compliance with occupational health and safety laws and regulations, related policies and our own in-house rules.
Occupational Health and Safety Promotion System
At Alps Logistics, we have set up the Companywide Health and Safety Committee under the supervision of the vice president in charge of administration, with the Human Resources and General Affairs Department serving as the administrative office. Working alongside the health and safety committees at domestic bases, the Companywide Health and Safety Committee promotes various activities related to occupational health and safety. The committee also provides monthly reports to the Board of Directors regarding the occurrence and status of any health and safety-related incidents.
Ryutsu Service and our overseas bases have also established safety management systems and are promoting relevant activities.
Measures and Initiatives for the Prevention of Occupational Accidents
Although the frequency rate of occupational accidents at Alps Logistics (non-consolidated) continues to be lower than the average in the transport and postal service industries, every year we hold a safety reinforcement campaign between April and July, a period when there are many new hires and redeployments, to further minimize the occurrence of accidents. Led by the Health and Safety Committee, we promote the following measures to prevent occupational accidents, with a particular focus on accidents where there is a risk of recurrence. At Ryutsu Service, we ensure thorough operation of the Shipping Safety Management System, and make ongoing improvements and enhancements through the work of safety supervisors.
[Occupational accident prevention measures]
- Implementation of occupational safety risk assessments through workplace patrols
- Production of in-house videos recreating real-life occupational accidents, and showing the videos at workplaces to reduce risk of recurrence
- Distribution of health and safety handbooks to newly assigned employees, and provision of education
- Promotion of prevention measures through communication of near-miss examples
- Regular confirmation of compliance with safety laws and regulations, and implementation of corrective and preventative measures when violations are discovered
Initiatives to Improve Safety Knowledge and Skills
Led by the Transport Management Department at the head office, we are working to improve driving skills and inspection techniques, and enhance awareness and knowledge of the importance of safe driving techniques through education, training, and internal and external study groups.
Acquisition of Excellence in Safe Driving Certification
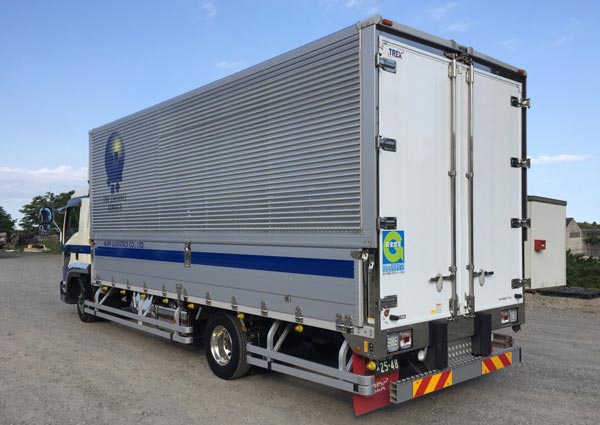
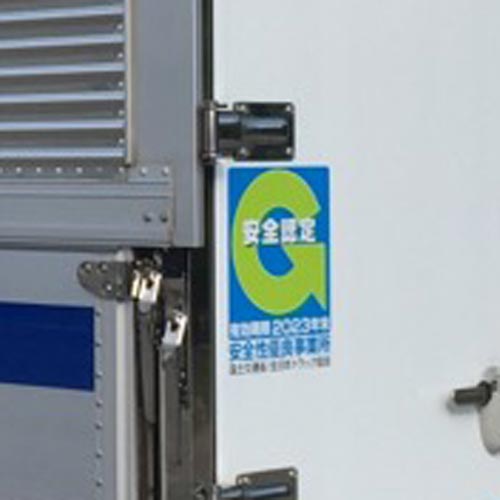
We are proactively working to acquire Excellence in Safe Driving (G Mark) Certification, which is awarded to offices with safe shipping operations. Ten of our 11 branches engaged in the transport business using company trucks continue to be recognized with the Safe Driving Certification. At our Nagoya Branch (Seto Branch at the time), which began transport operations in March 2022, we aim to acquire certification in 2025 after meeting the necessary criteria.
Hosting of the Forklift Skills Dojo
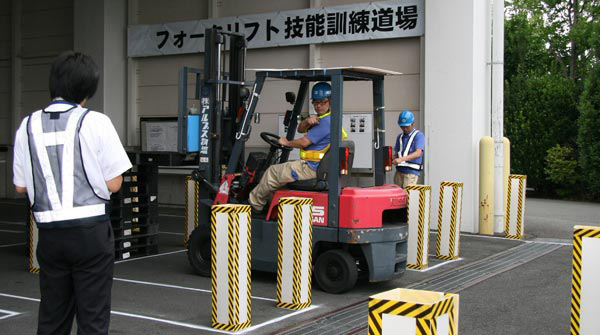
To maintain high safety standards, we require forklift operators to acquire a special in-house license. Forklift operators can acquire this license after completing classroom-based and practical training at the Forklift Skills Dojo. The license must be renewed every three years. Through this system, we aim to maintain and improve the effectiveness of our safety education. As of July 2023, approximately 430 employees at Alps Logistics and 730 employees at our partner companies hold this license.
Enhancement of Relationships with Partner Companies
At Alps Logistics, much of our transport network is covered by vehicles from partner companies, so we are working with these partner companies to promote safe driving. Every month we hold shipping meetings at each branch, sharing information on monthly cargo trends and distribution issues and promoting the horizontal deployment of accident prevention measures.
Health and Safety Data (Alps Logistics Non-consolidated; All Employees)
FY2021 Results | FY2022 Results | FY2023 Results | FY2023 Transport and Postal Service Industry Average*2 | |
---|---|---|---|---|
Frequency rate of occupational accidents | 1.2 | 2.3 | 1.8 | 3.95 |
Severity rate of occupational accidents | 0.04 | 0.02 | 0.03 | 0.19 |
No. of occupational accidents | 7 | 12 | 9 | — |
No. of traffic accidents*2 | 0 | 0 | 0 | — |
*1 Source: 2022 Survey on Industrial Accidents, Ministry of Health, Labour and Welfare of Japan
*2 As per Article 2 of the Vehicle Accident Reporting Rules
Health and Productivity Management
At Alps Logistics, we see the management of employee health and productivity as a key challenge. We are therefore promoting various health and productivity management activities, and working to improve implementation rates of regular health and stress checks among all employees in Japan as well as the follow-up health guidance. In October 2021, we formulated our Health Management Declaration.
Health Management Declaration
We consider the health of our employees to be an important management resource. Through proactive support for helping maintain and improve the health of our employees and their families, and systematic health promotion activities, we aim to become a company where employees can work with energy and enthusiasm.
Recognition as a Certified Health & Productivity Management Outstanding Organization
We were recognized as a Certified Health & Productivity Management Outstanding Organization (large enterprise category) under a program by the Ministry of Economy, Trade and Industry and the Nippon Kenko Kaigi for three years in a row.
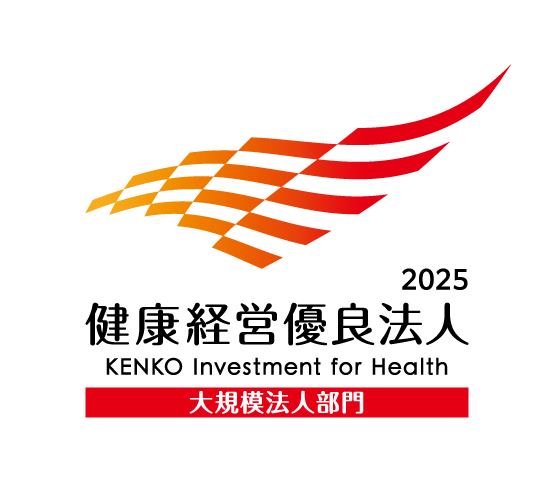
Initiatives | Overview |
---|---|
Walking events | As one way to improve employee health and encourage habitual exercise, we hold employee walking events twice a year. In FY2022, 341 employees participated in May and 412 in November. |
Reducing passive smoking | To minimize risks associated with passive smoking, we have moved our smoking areas outdoors and provide financial support for smoking cessation services. |
Infection prevention measures | To prevent the spread of infections, we take measures that include ventilating workspaces; encouraging employees to avoid closed spaces, crowded places and close contact; and regularly monitoring employee health through temperature checks. |
Initiatives | Overview |
---|---|
Employee Assistance Programs (EAPs) | We provide opportunities for employees to speak with counselors to address mental health issues or deal with fatigue as well as to find ways to improve their communication with colleagues and senior managers. |
Implementation and use of stress checks | Based on the results of statutory stress checks, we provide follow-up support to help employees notice signs of stress, encourage participation in EAPs and promote awareness and self-care. In 2022, 1,422 of 1,715 eligible employees underwent stress checks for an examination rate of 84%. |